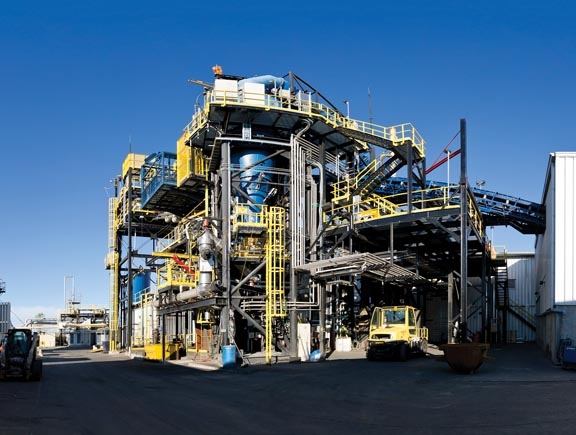
Emerging Waste Management Technologies: The Search for an Alternative
Waste management methods tend to vary by region, country and even county because of factors like economics and population density. Nevertheless, many different governments are arriving at the same conclusion: alternative sustainable practices need to be adopted—and soon! Landfills are reaching capacity and facilities are grappling with increased expenses. Hazardous fumes and emissions continue to rise, causing cities to look at balancing long-term environmental benefits with cost-effective methods.
The waste management industry overlaps with other industries like forestry, architecture, transportation, infrastructure and energy. There are also no standard definitions for industry terms like “municipal waste” and “industrial waste,’ creating implications for collecting data across countries. The most common waste treatment technologies are composting, incineration, landfills and recycling. All have their respective advantages and disadvantages, including incineration, which produces emissions of dioxins and furans. (Furan is a colourless, flammable, highly volatile liquid with a boiling point close to room temperature. It is soluble in common organic solvents, including alcohol, ether and acetone, but is slightly soluble in water. It is toxic and may be carcinogenic. Furan is used as a starting point to other specialty chemicals.) Alternative methods are making their way to a city near you.
Not surprising, waste management practices vary around the work. According to a World Trade Organization Workshop report by Dr. Jean Bogner, the waste management sector in developing countries is seeing increasing rates of privatization. Developing countries use a wide range of waste management practices and are evolving toward using engineered sanitary landfills and controlled composting. According to the United Nations Environment Programme (UNEP), developing nations are generating large volumes of electrical and electronic equipment waste, agricultural biomass and waste plastics. UNEP has established the Global Partnership on Waste Management for international agencies, governments, businesses, academia and NGOs that aims to “complement existing work in the area of waste” to reduce environmental harm, while overcoming social and economic issues. These are enough reasons to start considering what we should be doing differently. Many people do not like changing their old habits, including the ways they manage waste, but now it is time to do it. We must start handling it the right way, and for that, some companies have been redefining the business of waste management. All this by educating clients and making sure all your waste is categorized and disposed of adequately. At Away Today Rubbish Removal it is essential to get the most out of business and make it sustainable in the long run. Educating both people and governmental institutions will put us ahead as a society.
Dr. Bogner cited that nations including Canada, the United States, Mexico, Australia and New Zealand all use sanitary landfills and recycling, with low use of incineration, anaerobic digestion and mechanical biological treatment systems (MBT). Japan heavily uses incineration, recycling and landfills. Europe uses incineration, MBT, recycling and anaerobic digestion, and is evolving towards limited use of landfills. Countries export waste to other countries as a means to prolong the life of landfills or simply because they don’t have enough land to dump on. In 2001, Germany exported more than 300,000 tonnes of waste to 14 countries, while importing one million tonnes from 38 countries, with the largest volumes of waste coming from neighbouring European nations.
Ottawa has several waste management initiatives in place, including the green bin program, which is expected to divert 70,000 to 80,000 tonnes of waste from Ottawa’s landfills each year. The city also implemented bi-weekly household garbage pickup to encourage residents to recycle and decrease the amount of garbage at the curb.
Using a technology that converts solid waste into a synthetic gas, Plasco partnered with the City of Ottawa and Sustainable Development Technology Canada to build the Plasco Trail Road Facility, which recycles metals, provides water for reuse and recovers energy from waste otherwise destined for landfills. The process begins with Plasco’s patented technology that puts municipal solid waste into a conversion chamber to produce crude synthetic gas, using recycled heat. That gas then flows into a refinement chamber where plasma torches further refine it before it is sent through a Gas Quality Control Suite. Here, the sulphur, acid gases and heavy metals are removed to produce a clean, energetic synthetic gas, which is then used to fuel internal combustion engines and generate electricity. Waste heat recovered from these engines is combined with waste heat recovered from cooling the gas to produce steam, which can be used to generate more electricity.
Ottawa is also testing a new commercial waste project proposed by Taggart Construction Limited and Miller Waste Systems Inc., which is now under review. The plan includes recovering value from commercial and industrial waste, using a range of innovative methods. Masonry waste can be used for roadbed or other construction purposes, while wood can be turned into horticulture material like mulch or biofuel. For the organic waste, Miller is proposing to build an anaerobic digester. Microbes would devour the waste, producing a biogas with equal parts methane and carbon dioxide, which can be used to create energy like electricity or industrial fuel.
Miller’s current processing and waste diversion efforts reduce 80 per cent of waste from landfills at its Compost and Material Recovery Facilities for municipalities and commercial customers. The company owns and operates four compost sites nationwide that use indoor Ebara Technologies—a global, world-leading manufacturer of vacuum pumps—and windrow technology. (Windrow composting involves taking shredded feedstock, such as green waste, and forming it into long rows—called windrows—up to 3m high and 6m wide with a triangular or trapezoidal cross section. The windrows are regularly turned to mix and expose new surfaces to allow microorganisms in the material to convert the waste into compost. The process takes eight to 20 weeks.) Together, Ebara Technologies and windrow technology process 130,000 tonnes of Source Separated Organics and leaf yard waste annually. In 2008, Miller and Global Electric Electronic Processing Inc. formed a partnership to recycle electronic waste.
Toronto currently manages over one million tonnes of waste annually and recycles or composts 47 per cent of that waste. By 2034, Toronto hopes to reach a diversion goal of 70 per cent by implementing initiatives like a green bin organics program for apartments and condos, enforcing a mandatory diversion by-law, improving recycling capacity and establishing a biogas composting facility for mixed waste processing.
In the United Kingdom, Advanced Plasma Power uses Gasplasma technology, a gasification and plasma treatment, to convert waste into clean, hydrogen-rich synthesis gas and a recyclate product called Plasmarok. The synthesis gas can be used to generate electricity in gas engines or turbines. According to Advanced Plasma Power, Plasmarok will be used commercially in fuel cells within five years. Plasmarok is used mostly in construction because it can be made into tiles, slabs and blocks, or granulated for insulation material. The Gasplasma technology can process about 150,000 tonnes of municipal and commercial waste each year.
Alternative waste management technologies divert excess waste from landfills, recycle more material, generate energy and recover forms of heat. As countries continue to test these innovative practices to reduce their environmental impact, waste producers must support adoption of these advanced technologies and contribute to improving current systems. Paperless banking, recycling food containers and separating organic waste from other garbage are daily steps that make a collective difference.
Alternative methods include the following technologies:
Anaerobic digestion involves the use of microorganisms to break down biodegradable material when no oxygen is present. This method is commonly used for industrial waste. Organic polymers that are insoluble, like carbohydrates, are broken down for bacteria to access. Acidogenic/acid-forming bacteria convert sugars and amino acids into carbon dioxide, hydrogen, ammonia and organic acids. Methanogens then convert these into methane and carbon dioxide.
The bioconversion of biomass to mixed alcohol fuels converts biodegradable material into useful chemicals like carboxylic acids, ketones and biofuels. These acids include butyric acid, acetone, ethanol and propanol.
Biodrying also uses biodegradable waste, but heats it up rapidly through composting to remove moisture and reduce the waste's weight. This method can take only eight days to fully dry waste.
Gasification converts organic materials into carbon monoxide, hydrogen and carbon dioxide by reacting the material at extremely high temperatures using oxygen or steam. The result is synthetic gas.
Also referred to as aerated static pile composting, in-vessel composting systems use metal, plastic tanks or concrete bunkers to control temperatures and circulate air through buried tubes. This method is commonly used for municipal organic waste.
Mechanical biological treatment systems (MBT) combine a sorting facility with composting or anaerobic digestion and are designed to process mixed household waste, commercial waste and industrial waste.
Pyrolysis decomposes organic material at high temperatures without oxygen. Tyre pyrolysis converts plastic waste and tires into industrial fuels like pyrolysis oil, carbon black and hydrocarbon gas, which are used to generate heat, steam and electricity.
A waste autoclave uses heat, steam and pressure from an industrial autoclave to process waste in batches or a continuous flow. (An autoclave is a device used to sterilize equipment by subjecting it to high-pressure saturated steam.) For batches, steam is injected into the autoclave at about 160º C and maintained for 45 minutes to cook the waste. This process also kills pathogens and viruses.